Material model defines mathematically the relationship between deformation and stress state.
Elasticity and plasticity
Deformations are elastic when material will return to its initial form when loading is removed.
Deformations are plastic when material does not return to its initial form when loading is removed.
Linear elasticity
For linear elastic material the relationship between deformations and stresses is linear. Linear elastic material obeys Hooke's law
σ = Eε, where
- σ = stress
- E = young's modulus
- ε = strain
Real material
For real materials the relationship between deformations and stresses is not linear. In the figure below is presented an example of stress-strain curve for typical structural steel. Most metals behave linear elastic when stresses are less than yield strength.
In the figure below
- Yield strength
- Ultimate strength
- Breaking point
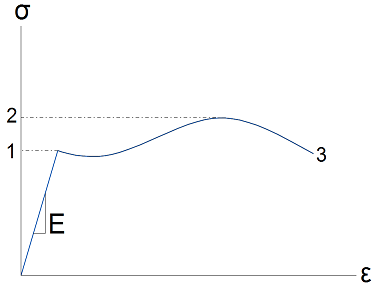
Yield strength
Stresses higher than yield strength cause plastic deformation in material. Material will yield when stress values are higher than yield strength.
Ultimate strength
Stresses higher than ultimate strength will cause the fracture of material.
Ductility of material
Ductility of material describes its behaviour in fracture.
Ductile material will always experience plastic deformation before fracture. The fracture of ductile material is usually easy to notice early.
For brittle material ultimate strength can be as low or even lower than yield strength. In fracture of brittle material there is no plastic deformation before fracture. The fracture may happen suddenly and it is hard to predict.